Let’s keep the detention but get rid of the pond.
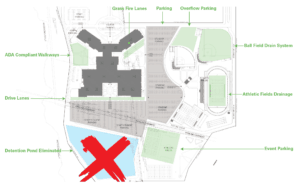
Storm water detention is an absolute must. As development and construction spreads, nature is bound and gagged by the spread of impervious surfaces – buildings and the ubiquitous excess of concrete and asphalt. The natural process of storm water infiltrating naturally unrestricted into soils and the water table and aquifers is halted by paved hardscape surfaces. The result of too much non-porous surface is flooding and the corresponding property damage and in extreme cases which are becoming more and more frequent, tragic loss of life. Detention ponds have been part of the solution to reduce flooding and protect homes and businesses.
The problem is that detention ponds are expensive and hazardous themselves. Detention ponds cost money to build, money to maintain and perhaps most importantly – take large chunks of land. Land that could be used for revenue generation now adds exponentially to the cost of a project. One of the main pain points for a developer is the amount and cost of his land that must be used for storm water detention.
Large 4 Acre Detention Pond Eliminated.
(Watch video below)
Now there is a better way.
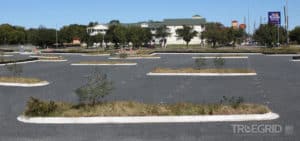
Put your storm water detention under the parking lot. With TRUEGRID plastic grid pavers filled with gravel on a rock sub-base, rain drains virtually instantly- over 800 inches per hour. The surface is 100 % pervious and the crossection of the sub-base rock and rock filled, TRUEGRID can detain stormwater. Using a clean, washed, hard, angular aggregate, typically a 57 stone, ¾’ to 1.5” in diameter, 40% of the void space between the rock across the entire crossection can be counted as detention. Drive on the surface and detain stormwater below in the rock sub-base.
How does one design a permeable parking lot with stormwater detention underneath the surface?
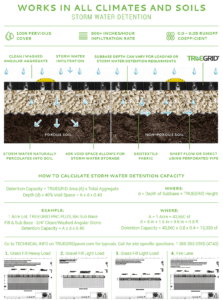
Step: 1: Determine the required detention capacity from your engineer. 2. Determine the square footage of your parking or driving area to be paved with TRUEGRID. 3. Multiply the square feet of grid by the depth of the crosssection (a typical commercial cross section has 8” of rock in the sub-base on top of the 1.8” grid which is also filled with rock). 4. Multiply the cubic feet by 0.40 (40%) and that gives you the stormwater detention capacity of your site. Click here to visit our technical specs page to download crosssections and other technical documents.
If more detention is required by code or per the engineered site plan, the depth of the sub-base can be increased to accommodate additional stormwater detention capacity. Although a 8” sub-base is typical, we’ve seen bases up to (4) feet deep. Most times the typical 9.8 “ cross section , 8” sub-base plus the 1.8” gravel filled grid, will provide the needed detention capacity. Add inches to the sub-base using the same formula to incrementally increase detention capacity.
How does one build a 100% permeable parking lot with storm water detention underneath the surface?
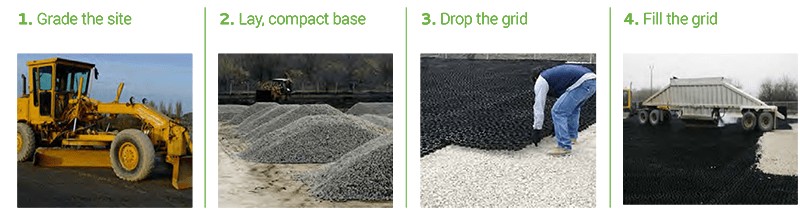
Step 1: Grade the subgrade soil to the depth of the desired TRUEGRID / rock crossection. Lightly compact or proof roll. (Note: do not install sub-base with wet conditions or standing water).
2. Lay and stretch a quality porous filter fabric that resists tearing but is porous to allow water infiltration into the soils. (Some areas may have non-porous clay soils that allow minimal infiltration. Typically outflow detained storm water by sloping the subgrade slightly and directing the out flow. Alternatively, adding a perforated pipe to collect, direct and outflow the water may be desired).
3. Lay the sub-base rock. Hard, washed angular ¾” to 1.5” rock. Do a heavy compaction in four (4) inch lifts. Level completely.
4. Lay the TRUEGRID permeable pavers on the rock sub-base. (Trim with a hand- held power saw to go around curves, curbs, trees, etc.) Make sure the transitions are level with or slightly below the surrounding landscape so only top load is applied to the grid pavement.
5. Back fill the grid with a washed hard angular stone, 5/8” to ¾” is best for high commercial, up to 1” for industrial sites. The empty grid can be driven on with an 18 wheeler full of gravel to dump the fill gravel so as to speed the installation process. The fill rock can vary to yield the desired aesthetic but should be hard, angular aggregate for high traffic or heavy load commercial parking lots.
Your 100% permeable TRUEGRID parking lot is now complete with detention below the paving. No lost land. The costly and hazardous separate detention pond has been eliminated.
Yes, you’ve saved money on construction and of course, you’ve saved a significant chunk of land. Yes, you can now build a larger building or add parking spaces (revenue generating impervious cover).
But here’s what else has been eliminated by eliminating your detention pond:
- Mosquitos – no more standing water from asphalt or concrete pooling or puddles. No more mosquito larvae breeding ground surface detention ponds.
- No long-term maintenance. Detention ponds often have pumps or drainage elements that need repeat maintenance. TRUEGRID is virtually maintenance free for the 40+ year life of your site.
- No thermal pollution from heat absorbing hardscape surfaces. No heated runoff streaming in local aquifers and waterways. Fish appreciate this more than you know.
- No toxic conditions from unmaintained detention ponds yielding pollutive toxins and bacteria.
- No more drowning hazard that needs to be secured. 6. And last but not least- no runoff from your pavement nor from your pond running into the aquifers and water table.
How can you eliminate your detention pond and save money?
Use the commercial grade, patented TRUEGRID PRO PLUS permeable grid system with a gravel or grass fill and a rock sub-base. Drive on the grid surface, detain storm water below. TRUEGID is as strong as concrete, cooler than asphalt and natural, and a naturally absorbent paving system.